News
Sustainable Innovations Used to Make CCLEX Possible
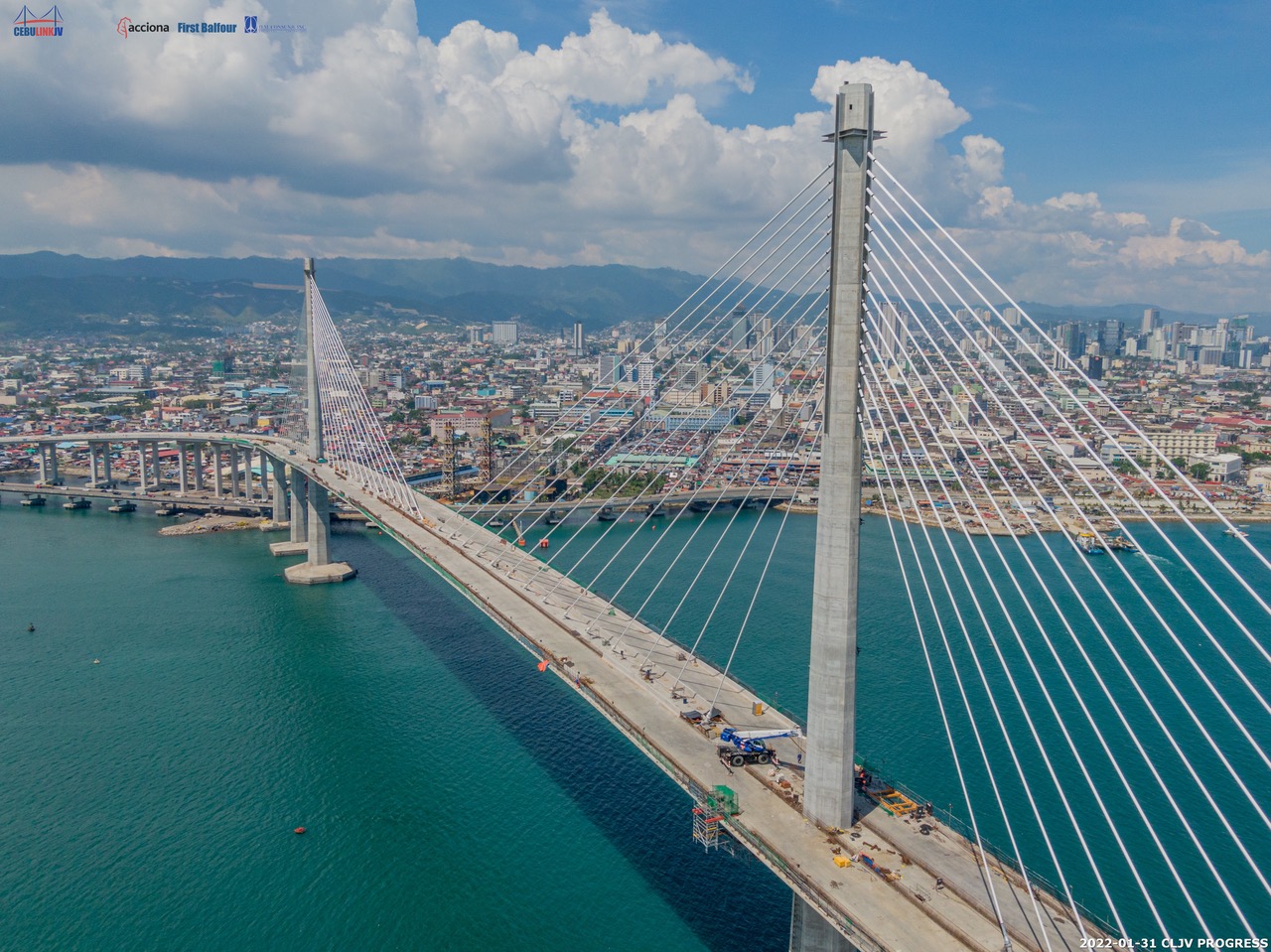
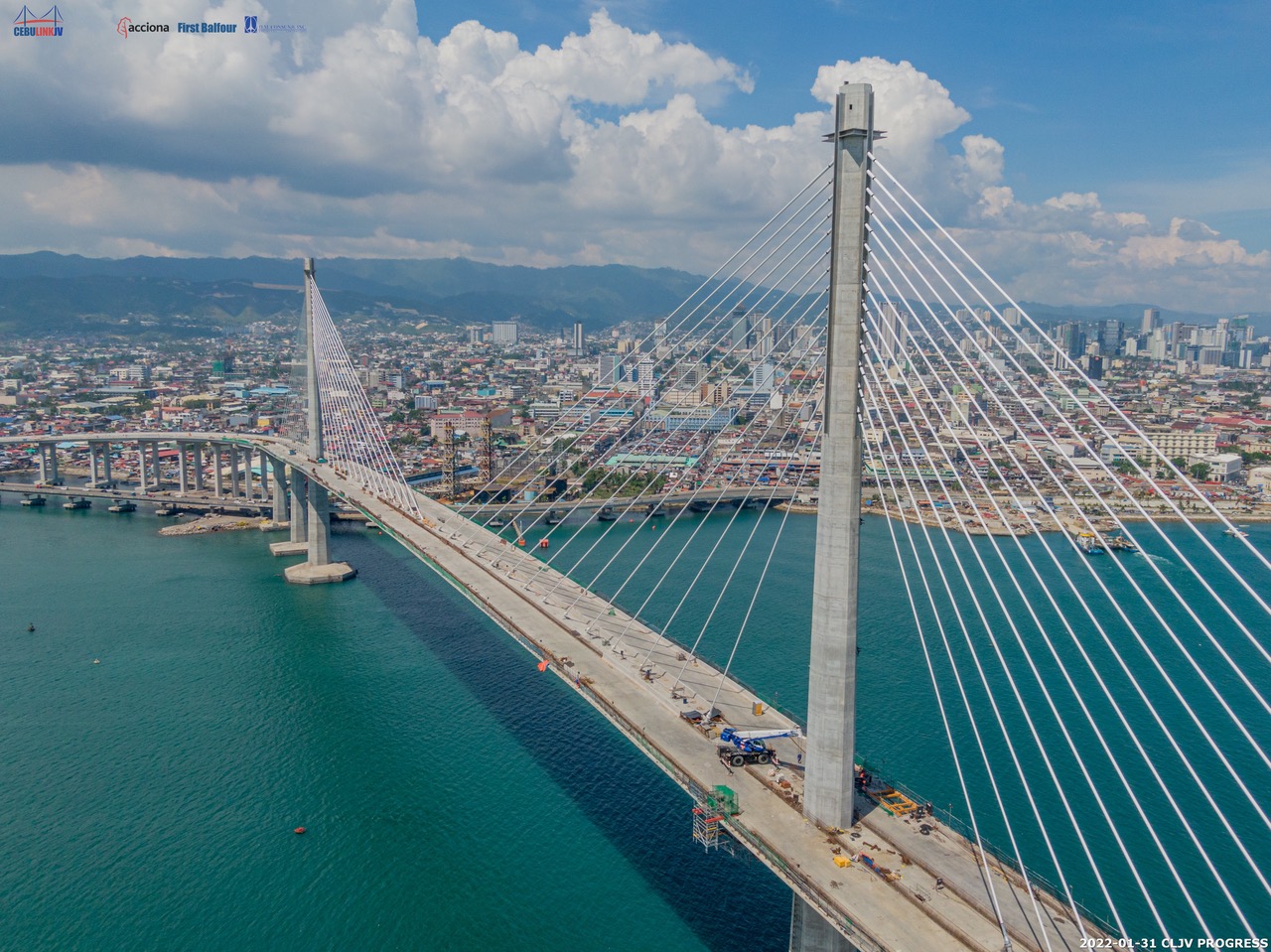
The Cebu-Cordova Link Expressway (CCLEX) is set to open this April 27. While CCLEX is already an engineering marvel, let’s take a deep look into the innovations involved in the construction of the longest bridge in the country.
ACCIONA, the Spanish global leader in sustainable infrastructure and renewable energy, revealed the sustainable innovations they implemented to make CCLEX possible.
ACCIONA made, designed, and transported a beam launcher from Spain that could raise beams weighing 110 tonnes, stretching 52 meters long, and with up to 7% gradients.
“The manufacture of the launcher took seven months and over 25,000 hours of work and consisted of an innovative rack-and-sprocket system that has become a benchmark in the sector. Its features give it better control while installing ramps and slopes and are safer and more precise than conventional winch and cable systems,” ACCIONA said in a press release.
Here are the innovations used for the construction of CCLEX:
Underwater foundations
The in situ concrete piles, which support the bridge’s pillars under the water, go down to 60 meters. They were built with the help of pontoons and vessels, which administered the cementing with a minimal impact on the seabed in the face of strong tides and the Channel current.
Metal jackets for construction support
To sink the piles 60 meters below the water, a metal tube or jacket was driven into the seabed to the design depth. Then a hole was drilled through the tube, and the concrete was poured. While the depth was a big challenge, reaching it via the sea was an even greater one.
Enormous pile caps
The construction of the framework for the octagonal element taking the load of the pylons required 3,500m3 of concrete for each of the pile caps. ACCIONA designed a cooling system to control the temperature of the huge concrete reaction and assure the specifications at all times during pouring and hardening.
A forest of steelwork and concrete
Managing 3,500 cubic meters of concrete in the pile caps was not only a challenge in terms of volume but also the difficulty in transporting it to the middle of the sea. Cement plants mixed the concrete on land and later carried it in pontoons to be pumped into the enormous formwork structures.
Building the pylons
If the pile caps represented a big challenge, building the two 145-meter-high towers, or pylons, on top of them was just as hard. The pylons were built using self-repairing formwork in 5-meter sections until the full height was reached.
Sustainable, versatile floating docks
The acquisition and preparation of the pontoons and vessels for executing tasks from the water was another challenge. Naval engineers calculated how much they needed reinforcing in shipyards or on-site to carry out the work and ensure worker safety. Many such seacrafts are not used to support such loads.
Stretching across the sea
Construction of the road on the bridge, or beam, was done in segments of 7.15 meters, concreted in situ, by moving forward the formwork with its support in the previously hardened section and later concreting — a process requiring a thorough study of structural behavior and geometric calculations.
Building in the air
For the in situ launch of the beam in concrete segments or sections, special formwork carriages, executing through progressive cantilevers, were used. The formwork carriages were launched, reinforced with steel, and filled with concrete pumped from an area next to the pylons. Once a section was hard, the carriage advanced to complete the next one.
The iconic cable webs
Cable-stayed bridges are called so due to the amazing strength given them by the metal stays joining the pylons to the beam. Fifty-six stays provide the bridge firmness and a unique architectural effect. The Cebu bridge towers have 14 guy cables connecting the pylon with the beam to compensate for the impact of strong winds and rain.
ACCIONA has created over 2500 jobs for local laborers. ACCIONA formed specialized teams for the construction of CCLEX.
CCLEX was built to celebrate the 500 years of Christianity in the Philippines. Its iconic pylons displayed 4 crosses reminiscent of the 500-year-old Magellan’s Cross.
CCLEX is a cable-stayed bridge with a 650-meter-long cable-stayed bridge that has about 400-meter span between its towers. This mega bridge is expected to cater to 50,000 vehicles every day. (ASC)